As an
approximate way to compare chassis designs a truss analysis program
has been used to run
comparative theoretical torsion tests.
The GRAPE GBW32
(Version 4.0) analysis program was used to run these tests.
For each
chassis a 3D DXF file was created in AutoCAD defining the particular
chassis geometry.
This was loaded
into GRAPE and materials, loads and constraints were applied.
The image below
shows the configuration of loads and constraints. The four corners of
the lower rear
chassis frame were constrained to be fixed in space. Two loads were
applied to the top front frame.
These were each 1000 lbs in magnitude, but applied in opposite
directions. The result was to apply a couple
to the front of the chassis (the two applied loads act to produce a
pure torsion). The specific material
properties for the tubing being used was loaded into the GRAPE
material
library, then applied to the respective chassis elements.
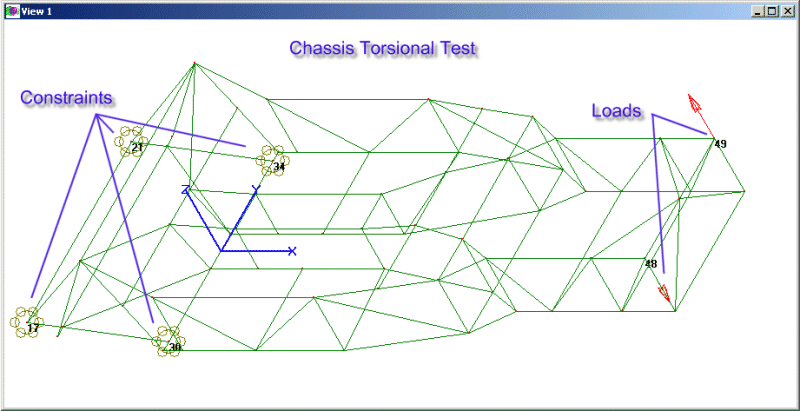
The practical
application of this to a real chassis is to mount the rear of the
chassis firmly to the ground then
apply an offset load to the front frame and measure the deflection of
the front frame under the applied load.
This is the basis procedure used to test the torsional strength of
real chassis. A number of example
chassis designs were tested in this way. A brief summary of the
results is as follows...
Chassis
Design |
Torsional
Stiffness |
Notes |
1
1X
2
3
3X
3Y
5
7A
7B
8A
8B
8C
9A
9B
|
1219
1129
1846
1787
2175
2161
1205
1787
485
127
161
152
187
200
|
Locost 7 with all square tube
Locost 7 Standard Chassis
All 25 mm square tube
All 25 mm square tube
Vertical RHS tube added
Horizontal RHS tube added
Backbone chassis
Backbone chassis
|
|
lbs.ft/degree |
|
The material assumed for these tests was C350 grade mild steel with the following
mechanical properties,
Property |
Value |
Young's Modulus of Elasticity
Density
Poisson's Ratio
Minimum Yield Strength
|
290 x 10^3 lb/sq.in.
0.2836 lb/cu.in.
0.25
50,762 lb/sq.in.
|
The Type 7, 8 and 9 chassis were part of a design exercise to see the
effect of different
layouts. These generally followed a path between the typical Clubman
space frame chassis and a backbone
chassis, as might be found in a Cobra-replica. All the designs used
25SHS tubing. The outcome of this test
is that a backbone chassis would be about twice the weight of a
Clubman chassis for a similar torsional
stiffness. The benefit of the backbone chassis is a body with
functioning doors can be used while a
Clubman requires entry over the side panels. A practical
backbone chassis will require heavy gauge
tubing in order to achieve acceptable torsional stiffness (much larger
than the 25SHS tubing assumed here).
|